Before
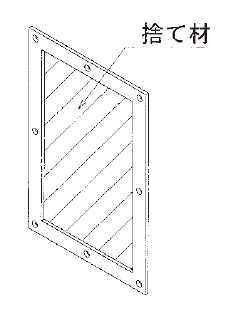
上記のように、長方形の内側に大きく穴が空いたプレート形状の製缶板金部品を製作する場合、レーザー加工によりプレート材料から穴形状を切り抜くことになります。この場合内側の捨て部分が不使用分となり材料歩留まりが悪くなってしまいます。材料歩留まりの悪化はコストアップにつながってしまいます。
コストダウン事例
After
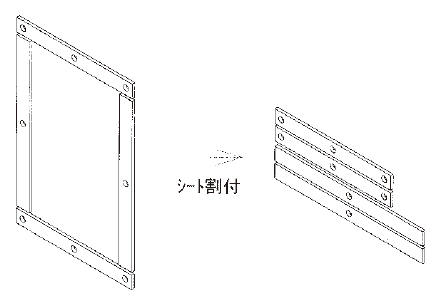
機構上問題が無ければ、上記のように製缶板金部品を4 つのパーツに分けた設計とすることでコストダウンが可能になります。この別体化の設計により材料から必要部材を効率的に切り抜くことができるようになり、材料歩留まりを向上させ、コストトダウンを実現することが可能になります。
大型の製缶板金部品においては材料歩留まりをいかに少なくするかということが設計段階で考慮すべき重要なポイントの一つになります。中央部に穴形状が存在するプレート部品の場合は単純に穴形状を切り抜くと材料歩留まりが悪化してしまうため、別体化構造を採用することで材料歩留まりを改善することができます。