Before
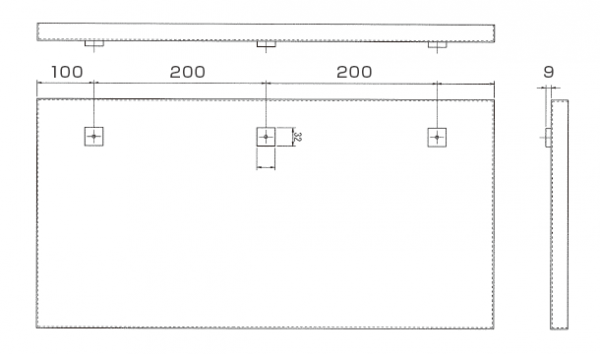
上図のように他製品を取付ける為のタップ座が最小限の大きさで複数取付けられる製缶板金部品は、見た目以上に加工に手間がかかります。まず、タップ座に使用する小さな部品はレーザーによる連続抜き加工時に機械の下に落ち、発生する火花によるスパッタが張り付いて加工終了時に人の手によるスパッタ取りを行なう必要があります。また、ボール盤によるタップ加工時には部品が小さい為、手で持つと危険なので保持できる台に取付けて加工することになり、個数分だけ工数が増えてコスト高となります。
コストダウン事例
After
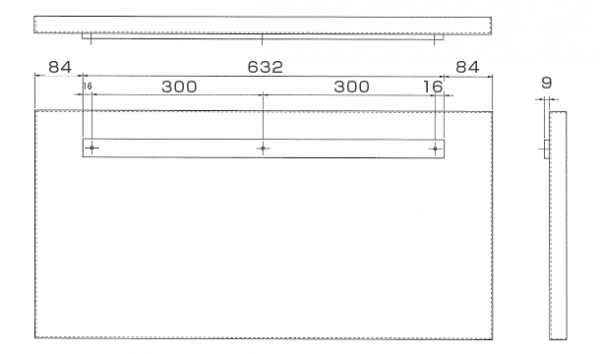
上図のように製缶板金部品の設計変更を行い、タップ座の部品を1 つに集約することで、レーザーによる抜き加工時に機械の下に落ちずスパッタが付着しません。また、タップ座の部品が大きくなるため、作業者は手で持ったままタップ加工することができ、加工時間が大幅に短縮されます。したがって、作業工数の削減によるコストダウンを図ることができます。
ボール盤などで小さな製缶板金部品を加工する場合は、作業者が手で押さえて加工するには危険なため治具を用意する必要があり手間がかかります。また、上記事例のようにスパッタの付着など、その他にも製缶板金部品が小さいことによる弊害は様々あります。当事例の場合は、部品を分ける必要性が低いため1つに集約することによって加工効率を向上させて工数削減によるコストダウンへと繋がっています。