Before
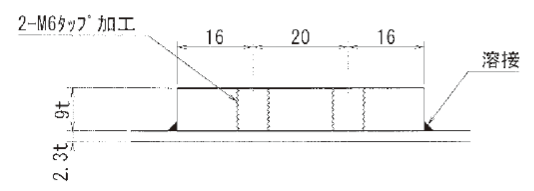
上図においては、2.3tのプレートにタップ穴の長さを確保するために、別途9tの板材を溶接しています。この場合、2 種類の板材を使用した製缶板金品となるため部品点数が増え、材料の調達・管理コストがかかることに加え、打抜き加工等もそれぞれ別途行う必要があるためコストアップの原因となってしまいます。
コストダウン事例
After
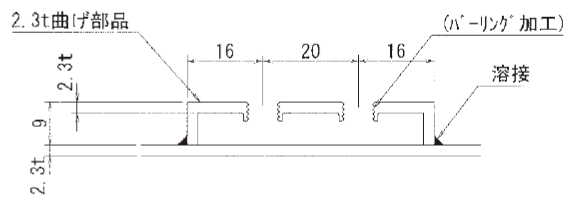
上図のように9tの板材の代わりに、2.3tのプレートをコの字型に曲げたものをプレートに溶接する設計へと図面を変更し、使用する板材を統一することでコストダウンを実現することができます。材料の共通化により、打抜きの加工が1 回で済むため、材料の調達・管理コストの低減と歩留まり向上によるコストダウンが実現できます。
製缶板金部品の設計においては、使用する板材を統一することで材料の調達コストと加工コストダウンを実現することができます。上記のような例ではタップ穴の長さを確保するために2.3t の板材に9tの板材を使用していたところを、2.3t の板材を加工した部品を溶接することで材料の共通化が可能になり、コストダウンが実現できます。